Eliche Radice: this is how a quality product is born.
If you asked a thousand people who has the greatest expertise in marine propellers you would always receive the same answer: Luca Radice. So who better than him to tell us in detail how they are created and what are the production stages of these very important products?
The creation of a propeller is a multi-disciplinary process involving design, engineering, simulations, testing and production to ensure that the propeller meets the thrust and efficiency requirements of its specific application. A product that even underwater is one of the most important elements for all boats, from simple tenders to superyachts.

Blade shape, rotation, thrust, angle of incidence are just some of the characteristics that distinguish propellers and their design. “The production of Radice propellers starts with the choice of material, which must be of excellent origin,” says Luca Radice.
For bronze castings (bronze-manganese and bronze-aluminium), Eliche Radice exclusively produces and uses its own alloys with registered names (Otman and Mibral) and approved by the various ship registers. For steels, different materials are used depending on the product, but they all come exclusively from suppliers certified and approved by the internal Quality System.
The molten metal, via a bridge crane, is transferred to the casting line. Here, through the use of filters that remove any traces of impurities due to the heat, the metal is cast into sand and resin moulds. Once this process is complete, all the propellers are transferred to the cooling room, where they remain for a whole day.

After waiting for the propellers to cool, they are passed over a detacher which, by vibration, separates them from the mould, and the sand re-enters the mould after being re-circulated through a cleaning and control process.
For this process, Eliche Radice takes samples of the sand used for casting and analyzes them again in the laboratory. Using a small oven, the resin is evaporated in order to control the specific weight of the sand and to be sure that impurity-free elements are fed into the production cycle.
The control is carried out twice a week precisely to have an immediate feedback of what is being produced and, in the event of a negative analysis, the production batch of propellers is discarded.
After being cleaned and checked, the propeller is then finished and passed on to the department, which will carry out a further check and test to certify its final quality.
Thanks to the product traceability, which is done by means of a bar code, the Radice propellers are classified, so that the mechanical test and date of production can be easily traced.
The desire of ELICHE RADICE to continuously innovate and to offer products of the highest quality, determines a continuous investment in technologies and new machinery; Luca Radice himself tells us that “7 years ago, with the advent of the new foundry and the market’s request to further reduce tolerances, investments of a few million Euros in machinery were made; in one year we bought 14 numerical control machines to make Class S propellers, the only system to be able to make them”.
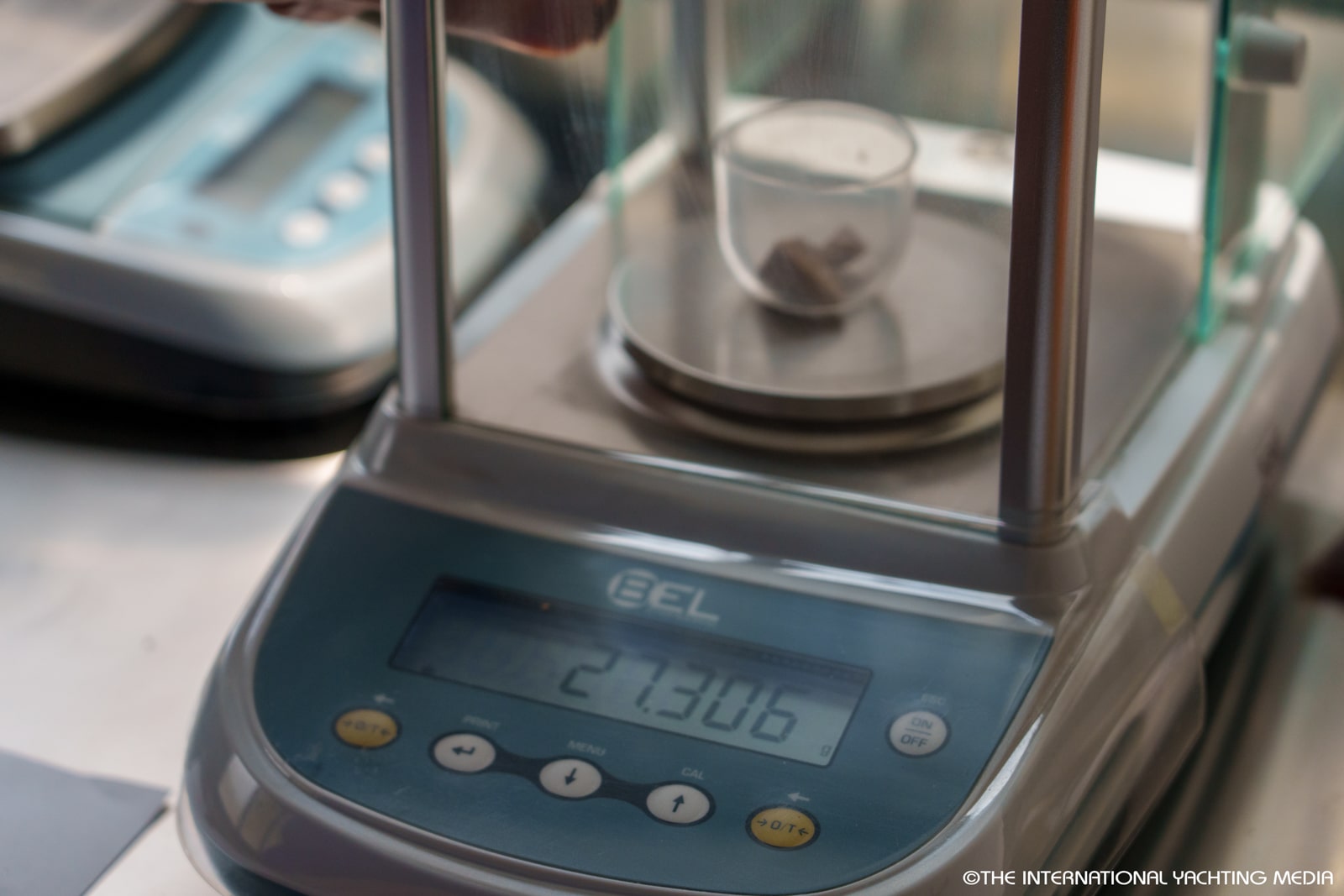
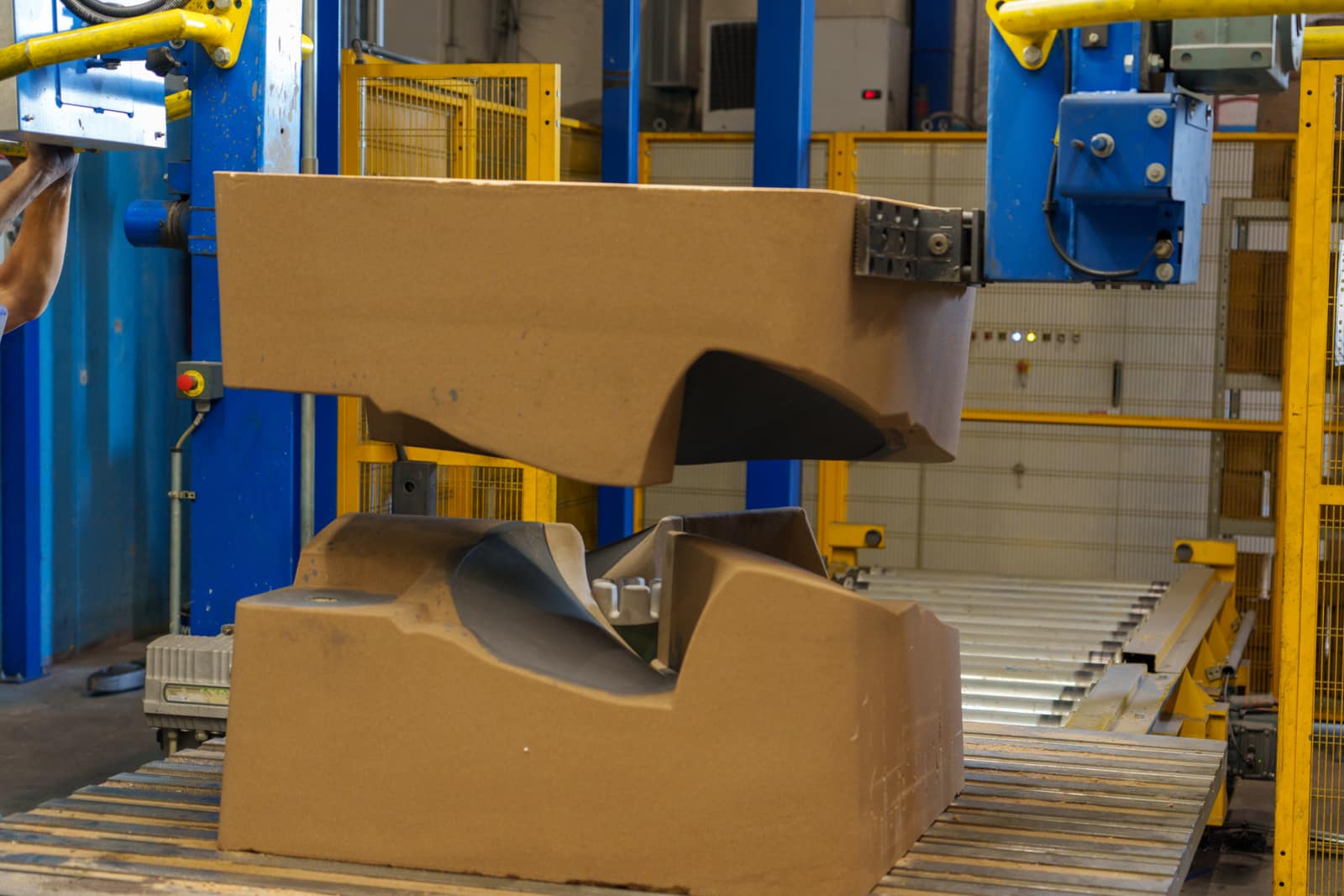
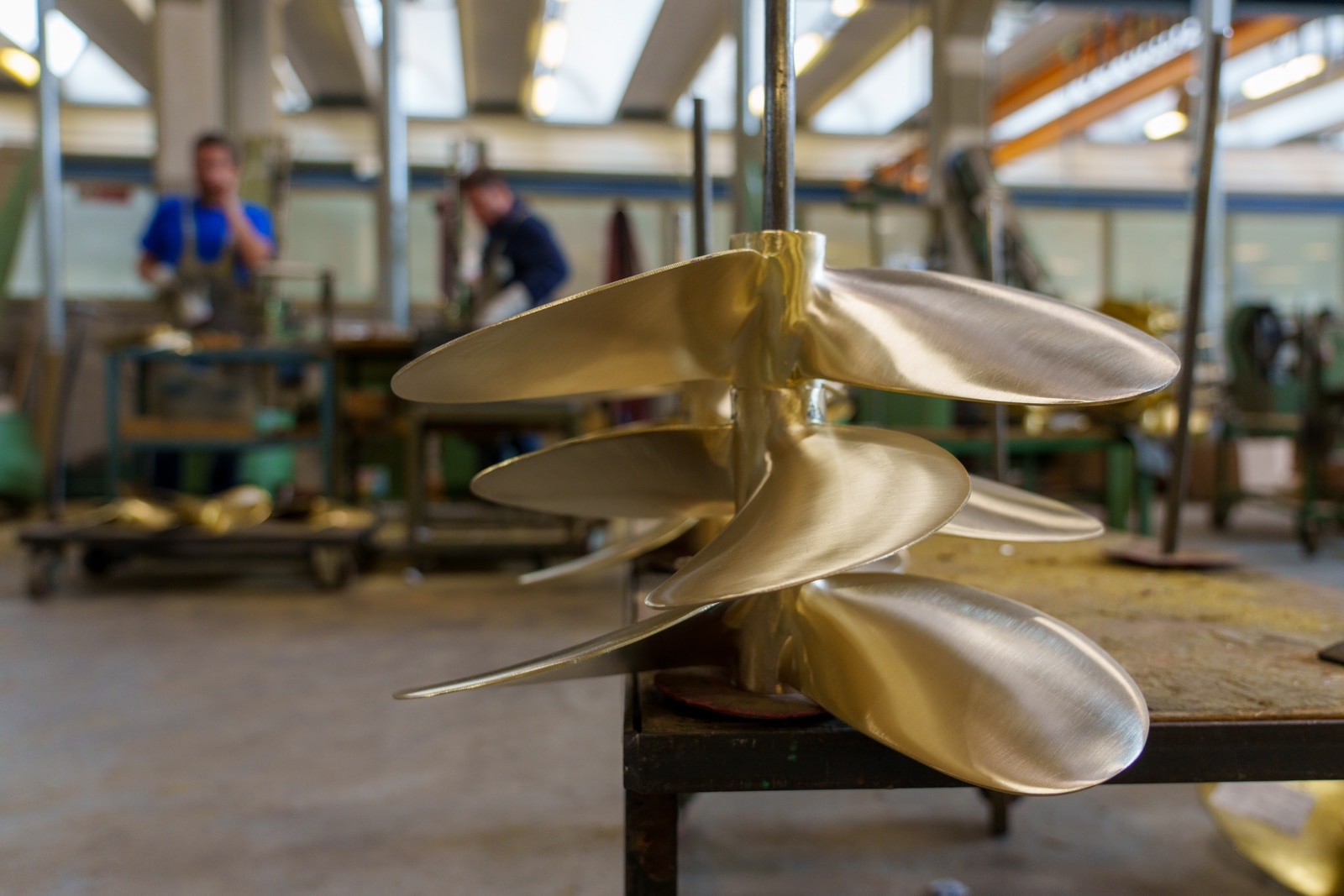
“Continuous renewal and improvement” is the motto that most identifies the company; with an area of 20,000 square metres today, it intends to further increase the production unit by a further 6,500 square metres.
Clearly, ELICHE RADICE is not “only” propellers, but supplies all systems and components for naval propulsion in yachting, military and work boats.
Axle lines, bushings, rudders, supports, flanges, casings, are entirely designed and manufactured in-house and thanks to continuous testing, the customer is certain to have supplies of excellent workmanship and guarantee. At the Dusseldorf GIFA trade fair, dedicated to the mechanical industry, the FONDERIA ELICHE RADICE will be presented as one of the most technologically advanced foundries in Europe.
Eliche Radice will be present at the Cannes Yachting Festival from 12 to 17 September at PAN 324.